How To Fight Back Against Occupational Diseases?
Workers from various industries worldwide have several differences in their social, physical, political, and economic environments. However, despite these discrepancies, they all face the same kind of hazards in the workplace. And when these dangers remain unaddressed for a prolonged period, they may develop into occupational diseases.
An occupational disease is an illness caused due to exposure or event in the work environment. At times, work-related hazards can worsen a preexisting condition or make individuals susceptible to other health issues. The World Health Organization estimates that almost 2 million people die from work-related causes every year.
Studies also show that the developing and the developed world share a disproportionate global burden regarding occupational hazards and injuries. This inequality likely stems from the preventive and safety measures implemented in industrialized countries in recent years. Therefore, we must address areas where occupational risks exist to minimize and control their spread.
Here, we have listed five ways you can fight back against occupational diseases to live a healthier lifestyle.
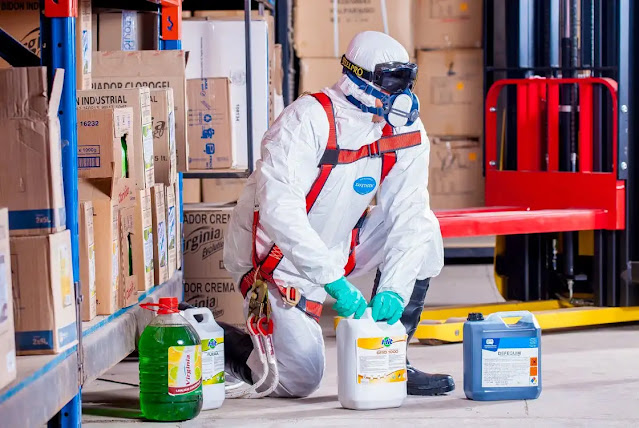
How To Fight Back Against Occupational Diseases?
1. Eliminating hazards in the workplace
The most effective strategy in preventing occupational diseases is to eliminate hazards from the environment altogether. With no immediate dangers in the work atmosphere, workers will no longer risk acquiring occupational diseases. For example, several countries have banned the use of asbestos in their industrial operations. However, if an organization continues to use it during any work process, employees have a right to file mesothelioma lawsuits and stake a claim for risking their lives.
Another example of eliminating hazards is to get rid of unwanted chemicals, pesticides, or detergents from your work environment. Additionally, you can reduce the risk of falling while cleaning windows from the outside by installing windows that open inside/out.
2. Substituting dangerous materials wherever possible
In some work areas, it may not be possible to eliminate hazards. For such cases, using safer and alternative materials, tools, or machinery is a better option. For instance, you can substitute asbestos with fiberglass in most of its operations and reduce the chances of contracting asbestos-related diseases. This practice minimizes the threat of occupational diseases and allows workers to perform their tasks in a secure environment. In factories and workshops where the noise of machines can get very loud, employees may have occupational deafness. To mitigate this problem, substitute the current machinery with low-noise machines to prevent further auditory damage to the workers.
3. Engineering control measures
Sometimes, neither substitution nor elimination can effectively minimize occupational hazards. Therefore, you can employ other control measures that keep the employees protected from surrounding dangers in these instances. Companies have adopted engineering control measures to manage hazards at their very source. Incorporating these within the equipment or a process ensures the exposure can be controlled—at least to some extent.
Engineering control measures consist of:
- Enclosure
Uses physical barriers to keep the hazardous material away from the worker and minimize its harmful effects as much as possible. It keeps the chemical “in” and the worker “out,” ensuring both are safe from the influence of one another.
- Ventilation
Installing a sound ventilation system can have two primary benefits. First, it brings in fresh air and creates a healthy workplace environment. Secondly, it extracts all potentially harmful or toxic substances present in the atmosphere and can cause adverse health effects.
- Process control
You can implement this strategy to alter the process or activity to minimize its risk and dangers. It may consist of wet methods to spray water on dusty surfaces to prevent dust from rising and causing respiratory irritation. You may also use automation rather than manual labor to keep workers from being exposed to potential risks.
4. Introducing administrative measures
In a workplace, employers and company managers must design safety management systems and a set of guidelines regarding the nature of work and its potential risks. By clearly outlining the details of each process, they must ensure all employees understand the dangers associated with each task. They must also emphasize the importance of implementing standard operating procedures.
Administrative controls aim to limit the amount of exposure time workers have to the hazards. Some examples include:
- Altering work schedules so that two people work on a task for two hours instead of one employee working for eight hours straight.
- Allowing workers to take more extended rest periods.
- Shifting a hazardous process to an area where there are lesser workers.
- Running a dangerous procedure at a time when fewer people are working.
5. Providing personal protective equipment
Controlling all potential hazards at the source is ideal for preventing occupational diseases. Compared to other strategies, using personal protective equipment or PPE is the least effective method in managing risks. Therefore, you should only implement it when the remaining plans are insufficient. When using PPEs, employees should receive special training on properly wearing them and regularly check them for damage, cleanliness, and hygiene.
PPE acts as a barrier between a worker and the hazard. However, the Occupational Safety and Health Administration (OSHA) guidelines recommend using them alongside other control measures as they’re not as adequate on their own.
Conclusion
Early symptoms of occupational diseases aren’t always apparent, due to which workers may neglect their health and delay treatment. Affected individuals often seek medical aid when the disease has reached terminal stages and treatment options become severely limited. Their health fast deteriorates, affecting work productivity and adversely impacting the morale of other workers in the company. But prevention is better than cure.
And it’s better to eliminate all potential risks rather than acquire an untreatable disease later. Therefore, employees and business managers must implement the proper control measures that can help fight against occupational diseases and safeguard workers’ health.
No comments